Elevator Law 101
Elevator laws are regulations that govern the construction, maintenance, inspection, operation, and modernization or repair of elevators and escalators. Though they vary from state to state and at the federal level, their primary purpose is to ensure the safety of those who use elevators and escalators, and those who work on them. The best-known federal elevator law, for instance, is the American National Standards Institute (ANSI) A17.1, Safety Code for Elevators and Escalators. This law is intended to ensure the safe installation, operation and maintenance for all freight and passenger elevators, dumbwaiters and related devices used for the movement of people and materials in buildings and structures. State laws regarding elevator safety have a similar focus.
Like the other building codes in the United States, elevator laws are based on an idea known as the "police power . " Castorina v. New York City Housing Authority, 7 Misc. 3d 1003(A) (Leadbetter, C. J., 2005), quoting Poirier v. Lubin, 34 Misc. 2d 137, 139-141, aff’d, 14 A.D.2d. 992 (1961). Police power allows individual states to create laws for the health, welfare, maintenance and regulation of private businesses and property in a given area. Castorina. So, elevator and building laws, generally, are intended to ensure the health and safety of individuals who spend time inside of a building or facility that has elevators or escalators. Castorina; Poirer, at 139; Greene v. Village of Rockville Centre, 68 A.D.2d 445, 445-446 (1982)("It has long been recognized that the regulation and scheduling of fire drills in public schools is within the police power of a municipality because it is reasonably calculated to protect the health, safety and welfare of school children.").
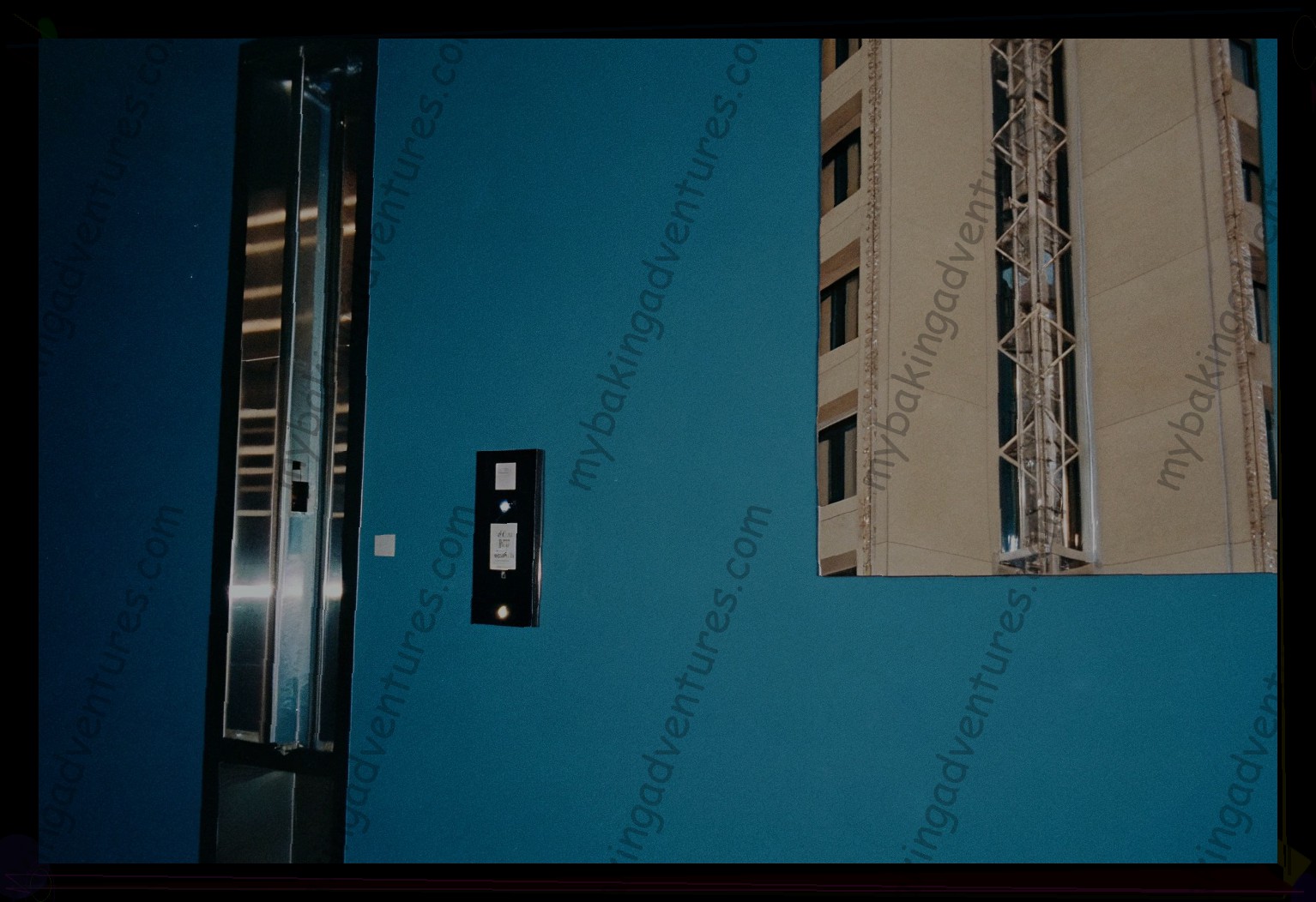
Elevator Laws on the Federal Level
On the national level, the Occupational Safety and Health Administration (OSHA) provides specific standards that govern the overall safety and maintenance of all types of electrical, service and freight elevators, escalators, dumbwaiters, moving walkways, specialized personnel lifts and personnel/materials lifts that support the use of powered industrial trucks (PITs). The primary OSHA standards that come into play for elevators are the US OSHA Oil and Gas Well Drilling and Servicing Operations Standard, General Duty Clause Standard, API RP 2I and API RP 8B.
The Federal Americans with Disabilities Act Accessibility Guidelines (ADAAG) also governs the accessibility of elevators in public accommodations and buildings. These rules set forth requirements for elevator operation and accessibility of elevators to give nondisabled individuals and those with disabilities access to the entire building and space. At a minimum, for all buildings with three or more stories, at least one elevator must be accessible to those with disabilities.
Since the passage of the ADA, the Building Officials and Code Administrators International, Inc. (BOCA), Council of American Building Officials (CABO) and Southern Building Code Congress International (SBCCI) have included the ADA guidelines in their commercial code. The BOCA National Building Code, CABO Model Code and SBCCI Standard Building Code now contain requirements mandating that buildings greater than three stories with elevators provide an accessible shuttle service for the upper floors for those who would otherwise be unable to access those floors without the use of a wheelchair lift.
While these federal laws impose minimum standards, state and local communities have the right to establish more exacting regulations concerning the installation and operation of elevators and escalators.
Elevator Laws on the State Level
In addition to a myriad of federal regulations that govern the inspection, testing, maintenance and compliance of elevators, most states have their own elevator laws. Even though certain safety minimums have been established at the federal level, those are just that: minimums. Complying with federal regulations does not mean you have also complied with any applicable local laws.
Most jurisdictions have adopted what is known as the "American National Standards Institute" (ANSI) code. However, specific requirements may vary from state to state and city to city. New York, for instance, has already adopted the 2019 edition of the ANSI code, which has not yet been adopted by most other jurisdictions.
Other states have adopted the "American Society of Mechanical Engineers" (ASME) A17.1 code, which is issued every six years to reflect new safety concerns, better technology and changing societal needs. States and cities also frequently adopt amendments to the code approved by their legislatures, as well as regulations that set specific requirements that vary from the approved code.
The level of elevator law enforcement also varies from one jurisdiction to another, as does the effect of violations on parties answering lawsuits involving injuries on the elevators that do not meet the minimum safety standards set out in the laws and regulations. Some states, like Florida, take an exceptionally strict view of elevators and things like the age of an elevator and the past inspections and history. Others, like North Carolina, while not permitting elevators older than 25 years to be installed, permit them to remain in service in buildings until they are 30 years old (older if permitted in specific other circumstances).
The different regional or local approaches to elevator safety regulation can baffle even highly educated and informed elevator professionals with many years of experience in the field. For example, many states and cities require the use of a 4-point choke for hoist ropes whereas others do not. There are very few pieces of equipment that even have 32 or 64 point chokes (which only exist for use on wires with many more strands – old-fashioned hemp ropes needed such small chokes because a brake was designed to grip only a strand or two of rope). It was unknown to some observers why some states like Florida and Virginia enacted laws and regulations that require the use of 4 and 8 point chokes for use in brake and emergency hoistway equipment. Eventually, those chokers will be difficult and costly to produce and will force some companies out of business.
If causing businesses to pay for equipment that does not conform to current norms is a concern, it should be possible to better fashion laws and regulations that achieve an admirable public safety goal without imposing extreme costs. It should also be the case that the expense incurred by compliance does not unfairly penalized a party to a lawsuit against a big corporation with the resources and skills to argue that the expense is unreasonable.
Elevators and Inspections
Elevators in high-rise buildings and other types of structures must be inspected and maintained to comply with both state and common law requirements. In Virginia, the Statewide Building Code requires compliance with the ASME A17.1 code for safety requirements for elevators and escalators. Elevators must be inspected at six month intervals but there are exceptions for certain classes of elevators. In Virginia, a comprehensive inspection at 100 percent test load is required every five years. The Comprehensive Inspection includes testing the safety devices and emergency features and observing the operation of the elevators. At the time of the inspection, the elevator inspectors will issue an appropriate Certificate of Inspection. Maintenance of elevators must be performed at intervals that ensure each elevator will be operated in conformity with the requirements of the edition of the ASME A17.1 code applicable at the time the equipment was installed.
Liability and Compliance
Navigating the maze of elevator laws can be a daunting task for many construction professionals, particularly when it comes to compliance and potential liability. Failure to adhere to the relevant state or federal building codes can result in financial penalties, forced remediation work, or even worse – a catastrophic incident that causes loss of life or serious injury. In the highly regulated construction industry, building professionals have a statutory duty to comply with all relevant laws and standards.
These laws and standards are as numerous as the types of projects themselves. Each state has its own individual building codes that builders must follow. Subcontractors are typically responsible for complying with the building codes that are specific to the portion of the project they are able to complete. However, the general contractor on a project remains responsible for overseeing the entire project from start to finish, so it is important that they have an understanding of these requirements.
In addition to state building codes, the U.S. Department of Labor has prescribed regulations that apply to freight elevators, dumbwaiters, and inclined automatic stairway or escalator lifts. The Occupational Safety and Health Administration (OSHA) , the agency of the U.S. Department of Labor, establishes these regulations as mandatory for construction sites. Regulations also mandate minimum safety standards for elevators in the public or semi-public use.
Nationally recognized industry standards are not the law, but they can be used in many cases as the benchmark for standard of care. There are nearly thirty model or consensus standards dealing with elevators and escalators that have been developed by organizations such as the American National Standards Institute (ANSI), the National Fire Protection Association (NFPA), the American Society of Civil Engineers (ASCE), and the American Society of Mechanical Engineers (ASME). These standards set forth recommended maintenance and inspection requirements for this type of machinery.
Given the extensive legal requirements associated with the use and maintenance of elevators and escalators, construction professionals must be vigilant in following all applicable laws, regulations, and standards. Compliance is imperative to avoid conflicts with the law that could result in monetary penalties or even imprisonment, and to ensure the highest possible quality of work.
Recent Trends and Changes in Elevator Law
Recent changes in elevator laws reflect the rapid pace of technological advancements in the field of elevator and escalator both in operation in the whole world and those currently being developed, which are in advanced stages of development such as smart elevators. All over the world, although different nationalities have different technologies, these technologies continue to advance, improve and become incorporated into the main system. These changes are reflected in two general ways, namely, by creating new laws and that existing laws are augmented to include new possibilities and scenarios.
One of the technological advances in the manufacture and operation of elevators that has led regulators to amend existing laws and issues new laws is the introduction of smart elevators. One of the purposes of this kind of elevator is the flow of people. They have features such as faster travel time between floors that will become a characteristic of most elevators and, in addition, they will allow users to program destinations and not only buttons of call. One of the American companies that is leading the change to smart elevators is Otis. These technologies have emerged working on theories of traveling time and flow of people based on the variability of traffic patterns in a building, taking into account the profiles of users. This is, in fact, the approach of each of the routes assigned to the elevators of a building based on the traffic pattern of the same.
Another important aspect that has influenced the amendment of elevator laws is in the areas of safety. Directors and safety officers consider that there is a gap between the development of new systems and their identification by emergency personnel. In this way, safety systems, general alarms, emergency signals, elevator positions and other mechanisms of the elevator must be brought to the application and knowledge of any emergency personnel.
The Future of Elevator Law
As we look into the future of elevator laws, several potential scenarios present themselves. First, the evolution of the Internet of Things (IoT) will likely see elevators as networked components of the urban infrastructure. Elevators will not only transport people, but also monitor and report their own operational efficiencies while providing real-time information about their usage.
We might also see an increased emphasis on sustainable technologies. Innovative solutions such as regenerative drive systems, solar panels , and smart air circulation might no longer be add-ons for new buildings but mandatory requirements for older structures as they are remodeled or updated to meet new codes and regulations.
The rapid growth of the urban infrastructure and its diverse vertical and horizontal spaces has increased the focus not only on private-sector buildings but also on public-sector spaces.
We may see greater attention on multi-use spaces. For example mega buildings such as hospitals that have traditionally been separated into distinct wings or sections, and which have had separate elevators for each area, might under future regulations be required to configure and to create multi-purpose elevators using the IoT to monitor and manage their schedules of use.
The future of elevator regulations is difficult to predict given how quickly technology has advanced in the last few years, and how this technology is evolving at an increasingly faster pace. Those who regulate this technology must keep up with these changes.